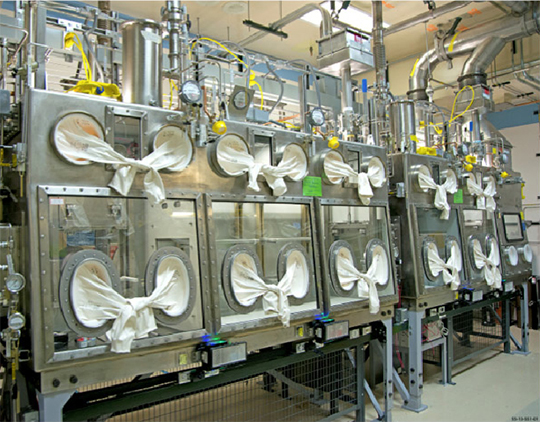
Nuclear Security & Deterrence Monitor Vol. 27 No. 41
Visit Archives | Return to Issue PDF
Visit Archives | Return to Issue PDF
Nuclear Security & Deterrence Monitor
Article 1 of 7
October 27, 2023
Plutonium mission stressing NNSA glovebox supply chain
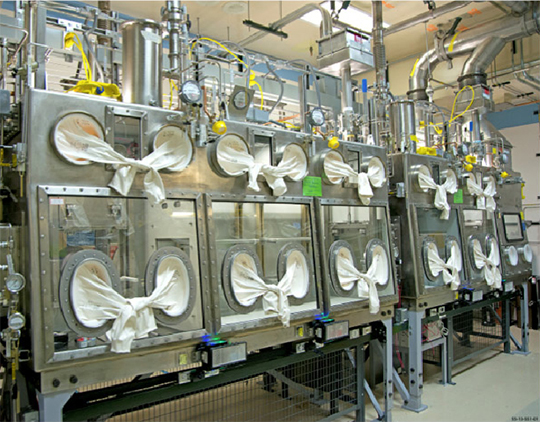
The race to build 80 nuclear weapon cores per year is stretching the U.S. supply of gloveboxes used to keep engineers radiation-free while manipulating plutonium and other hazardous materials.
The equipment is becoming difficult to source, Michael Robinson, vice…
Partner Content